《高效精准模具设计软件赋能智能制造新突破》
adminc2025-03-23常用软件32 浏览
模具设计的未来:高效精准软件如何改写智能制造规则?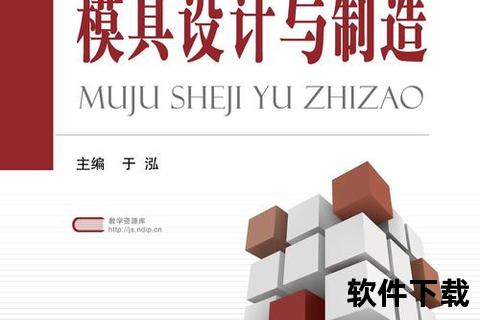
在全球制造业向智能化转型的浪潮中,模具设计软件的角色正悄然发生剧变。过去,模具设计依赖工程师“手把手”操作国外高端软件,设计周期长、成本高,甚至面临技术封锁的“卡脖子”风险。而如今,国产智能设计软件异军突起,不仅效率提升20倍以上,还能自动规避设计失误,引发行业热议:高效精准模具设计软件赋能智能制造新突破,究竟是概念炒作,还是真正颠覆传统模式的利器?
一、国产软件能否突破“卡脖子”困境?
长期以来,达索、西门子等国外CAD软件占据中国模具设计市场90%的份额,高端复杂模具设计几乎被垄断。这种依赖导致企业支付高昂授权费,甚至因技术封锁影响生产。而大捷智能推出的Agle Mold软件,通过几何特征智能识别、参数化混合建模等核心技术,实现了“弯道超车”。
以汽车机盖外板模具设计为例,传统国际软件需12~15天完成,而Agle Mold仅需半天。其核心在于:
1. 工艺驱动自动化设计:导入冲压工艺数据后,软件自动识别关键参数,生成凸凹模本体等结构,减少80%的手动操作;
2. 智能标准件库:内置主流品牌标准件,结合运动包络分析,一键布置效率提升20倍;
3. 内嵌性能评价算法:铸造可行性、结构刚性等评估模型,将设计失误率降至零。
某家电企业应用Agle Mold后,模具设计成本降低75%,调试周期缩短60%。这不仅打破了国外技术壁垒,更证明高效精准模具设计软件赋能智能制造新突破已从理论走向实践。
二、参数化建模如何实现“千人千面”的定制需求?
模具行业长期面临“单件订制”难题——每套模具结构相似却需重新设计。CATIA参数化建模技术通过定义尺寸、材料等全局变量,让“一图多用”成为可能。
案例1:汽车底盘快速变型
某车企开发SUV底盘时,调整轴距参数后,软件自动更新悬架位置、传动轴长度,设计周期从2周压缩至1天。案例2:工业阀门定制:输入压力等级、口径等参数,系统生成符合ASME标准的3D模型,错误率降低90%。
这种“逻辑驱动”模式,将工程师经验封装为规则库。例如,当产品长度超过阈值时,软件自动增加加强筋;材料强度变化时,壁厚参数同步调整。美的集团在注塑模具中引入参数化技术后,设计效率提升40%,客户定制响应时间缩短50%。这标志着高效精准模具设计软件赋能智能制造新突破已从标准化迈向个性化。
三、数字化检测如何让误差无处遁形?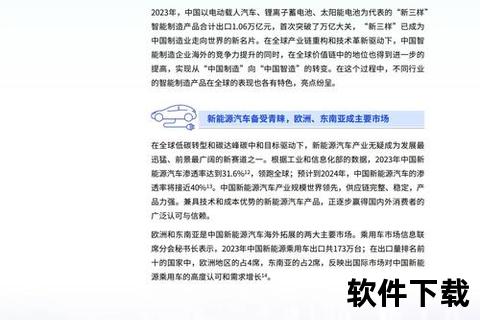
传统模具检测依赖人工涂抹染料,耗时长且精度低。思看科技的TrackScan-P三维扫描仪,10分钟即可完成汽车铸铝件模具检测,精度达0.025毫米。其突破在于:
非接触式扫描:避免模具表面损伤,延长使用寿命;
合模模拟分析:上下模数据导入软件后,自动生成干涉报告,提前规避装配风险;
云端协同:检测数据实时共享,支持多地团队同步优化设计。
某铝合金轮毂企业应用该技术后,模具损耗成本降低30%,产品不良率从5%降至0.3%。数字化检测与智能设计软件的结合,让模具从设计到制造形成闭环,真正实现“零缺陷”目标。
从工具升级到生态重构:企业如何抓住机遇?
高效精准模具设计软件赋能智能制造新突破已不再是孤立的技术进步,而是推动全产业链变革的引擎。企业若想把握机遇,需采取以下策略:
1. 优先选择国产平台:支持Agle Mold等自主软件,降低供应链风险;
2. 构建参数化知识库:将工程师经验转化为规则,提升设计复用率;
3. 推动数据贯通:打通设计、检测、生产数据流,实现全流程数字化管理。
正如上汽大通通过C2B模式让用户参与设计,未来模具行业也将走向“用户定义制造”。唯有拥抱智能软件技术,才能在效率、精度、灵活性三维度赢得先机。